Analysis on the Control and Influence of Trivalent Chromium in Chrome Plating Process
Trivalent chromium is one of the main compositions of
colloidal membrane which generates on the surface of cathode in chromium
plating process. The certain amount of trivalent chromium in the chromium
plating solution can improve the throwing power of the solution. Only when
moderate amount of trivalent chromium exist in the plating solution can possibly
get the bright and perfect chromium layer, or chromium plating will not achieve.
When the content of trivalent chromium in the plating
solution is too high (the range is between7g/L
and l0g/L), the surface of
cathode will be covered by a alkaline Dichromiumtris(chromate) mucosa layer,
which is composed by trivalent chromium and hexavalent
chromium. With the sulfate radical dissolve mucosa layer slowing
down, which will control the reduction
reaction of hexavalent chromium on cathode. If the mucosa layer
is dissolved off and the matrix exposes, the actual current density of metal
reduction will higher than that the best region needs, which will cause hard
spots, turn gray or white, or even rough layer on the surface.
When the trivalent chromium reaches a value higher than l0g/L, the conductivity of solution will
decline, the resistance will increase, the solution will turn black, and the throwing
power and covering power will get bad obviously.
Trivalent chromium mainly increases for the following
reasons:
1. When
the cathodal area is larger than anodal area, trivalent chromium will increase
gradually. This is because the oxidation reaction is less than the reduction
reaction.
2. As the
chromium trioxide is strong oxidant, all polishing factice and other organic
impurities in the plating tank can be oxidized. The hexavalent chromium will be
deacidized to trivalent chromium soon.
3. When
the content of sulfuric acid is too high in the solution, the trivalent
chromium will combine with sulfuric acid into Cr2(S04) 3, making the trivalent chromium difficult to be oxidized in anode, and
the trivalent chromium will gather and increase.
4. When
the temperature of solution is too high, the generating speed of colloidal mucosa layer will decrease, and the trend
that hexavalent chromium deacidizes to trivalent chromium in cathodal
area will increase.
5. When
the content of iron impurity in the solution exceeds4g/L, the trivalent chromium will be very hard to be
oxidized to hexavalent chromium.
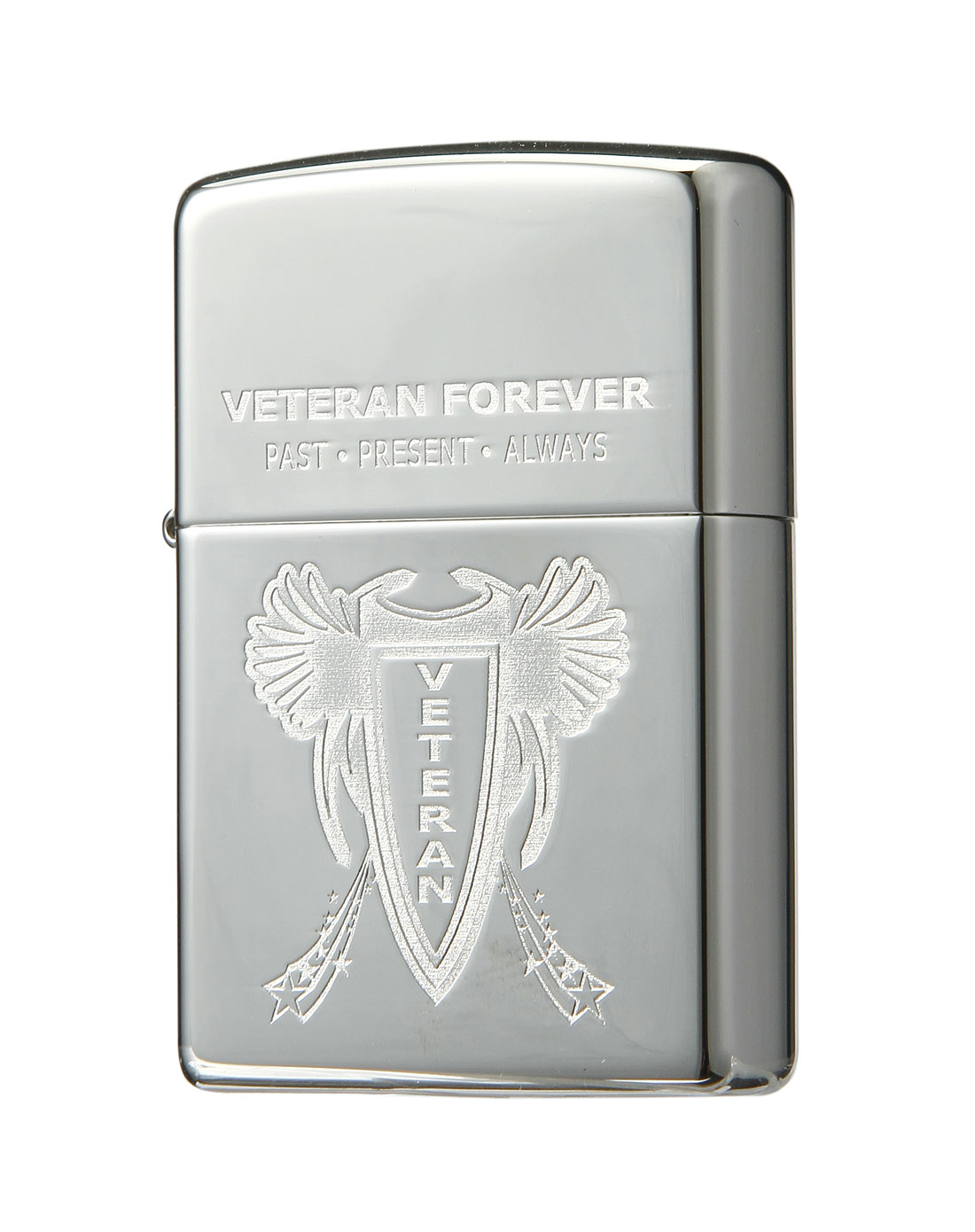
To regulate the content of trivalent chromium in
solution, the following methods can be adopted:
1. Energizing,
when the iron impurity content in solution is not high, energizing can be adopted
to make superabundant trivalent chromium be oxidized to hexavalent chromium. During
the energizing process, it need to adopt rustless iron plate in cathode, making
the anodal area be 5 times larger than the cathodal area, keep the anodic
current density to be 1~2A/d㎡ and
keep the temperature to be 50~60℃. It need
about4 A·h when the trivalent
chromium declines1g, and
it can be regulated to a normative level according to the content of trivalent
chromium.
2. Oxidizing
with hydrogen peroxide. When the content of iron impurity is relatively high
and the trivalent chromium is not easy to be oxidized in anode,
hydrogen peroxide can be used to oxidize it first, and then use the electrolytic
treatment together. Before the above processes, the temperature of solution can
not higher than45℃and the sulfuric acid need to be subsided in
advance. During the process, hydrogen peroxide should be added slowly, in case
of that the solution spill out because of adding too fast.
3. Dilution,
dilute and regulate it according to the calculated amount. To prevent the increases
of the trivalent chromium, eliminate the greasy dirt and organics polluted
solution, the key is that we should always keep an eye on regulating the
current density of cathode and anode, and keep the area of cathode and anode
maintain the proportion on 2:3.
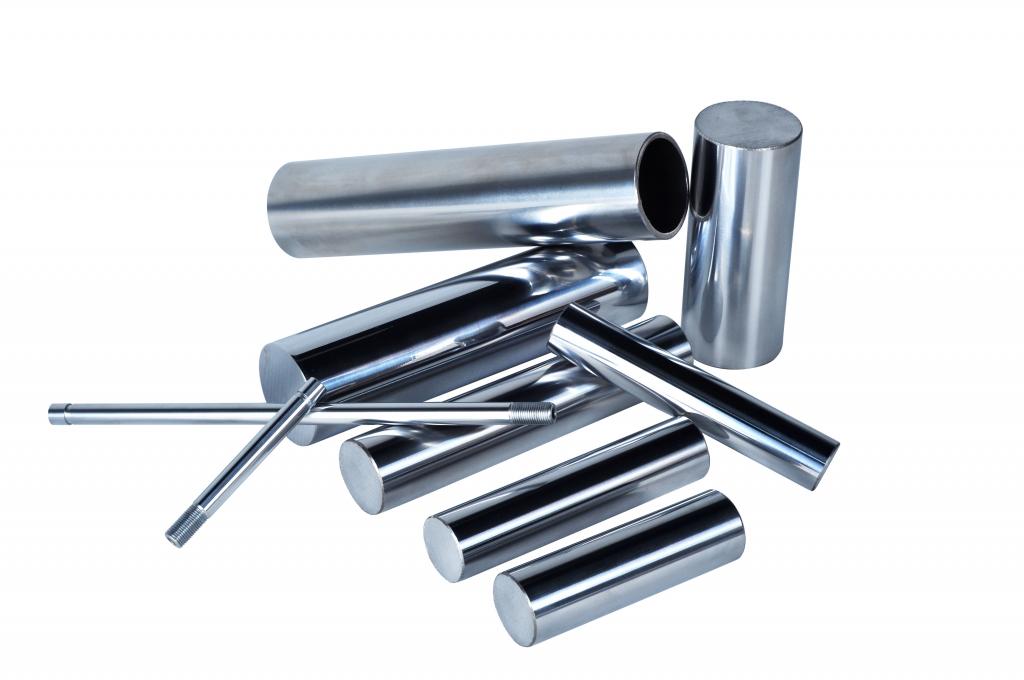
Product recommendations:
1.
HN-82 High speed decorative chromium plating process:
Adopting
the easy-controlled soluble and mixed catalyst, it has high tolerance against
impurities and easy to operate; has higher current efficiency of cathode and
deposition velocity, can operate under high current density; components can be
activated well and has wide brightening range; with excellent covering power
and dispersive ability.
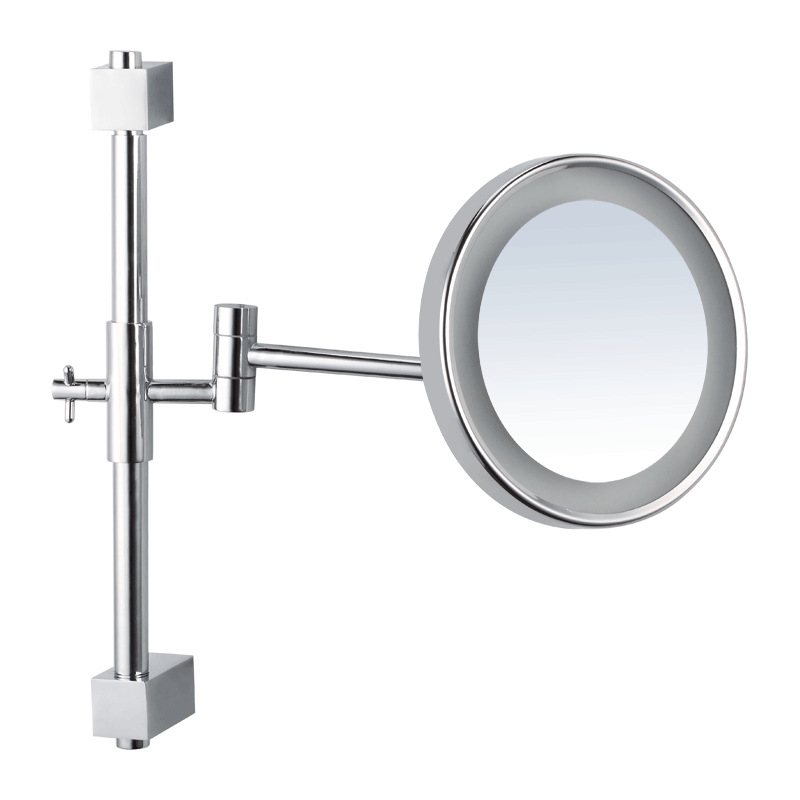
2. HN-25 Hard chromium
plating process:
Adopting
the unique formula, no fluoride, it won’t corrode the low current area of the component;
it won’t corrode tin-lead anode and is not require special anode materials; the current
efficiency of cathode is high, can reach 22~26%; has even, fine and bright
deposit; has high micro hardness of deposit and good corrosion resistance.
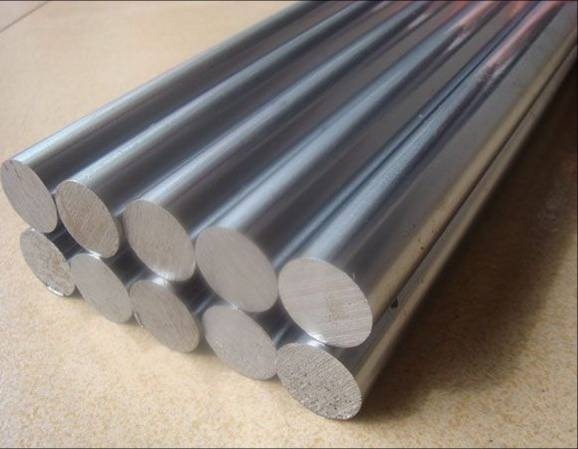
3. HN-09 Hexavalent black
chromium plating process:
Adopting
the easy-controlled soluble and mixed catalyst, it is easy to operate; use
pb-sn-sb anode to improve the quality of deposit and the stability of plating
solution; the coating color is uniform and bright with good covering power and
distribution ability; has good corrosion resistance and high-temperature
resistance, the black chromium layer won’t change color and get crisp even when
the temperature rises to about500℃,
has good thermostability; be widely used in protective decorative chromium
layer which work for deceasing reflectance or functional layer which has
special demand, such as the applications in the area of light industry,
instrument, aerospace.
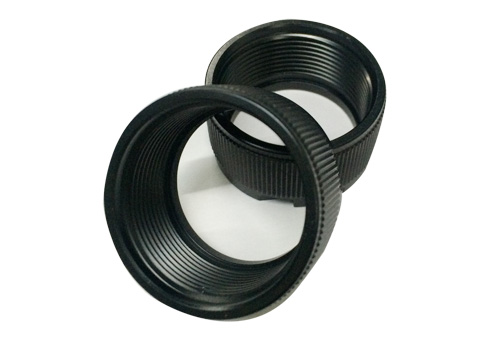
4.
HN-701 Chromium fog inhibitor:
It is a chromium fog inhibitor specially designed for
chromium plating. It not only can eliminate the environmental pollution coming
from chromium fog, reduce the maintenance costs of exhaust equipment and the
dosage of chromic acid, but also can decrease the microcrack degree, improve
the chromium layer hardness and promote the adhesion.